When the design of a low-voltage electrical panel begins, among other things, we face the decision about how to make the power distribution. We have two ways: either using wires or opting for a busbar system. Let’s analyse which are the aspects to be considered in order to make the best decision.
What standards say
The first thing to do is to look at standards. In this case, the standard is EN 61439-1, which regulates the low-voltage switchgear and controlgear assemblies. According to the standard, there are no situations in which we are forced to use one solution rather than the other, but there are thresholds above which it is necessary to verify the short-circuit resistance. In these cases, having busbar systems makes things much easier. The standard requires the distribution system to be tested directly or to be verified by comparison with a reference design. In this case, the use of a busbar system is advantageous, given that normally the manufacturers have already made a series of tests for the various configurations. The comparison can be made either with a checklist contained in the standard or through calculations. In any case, the system must have the same or better characteristics than the tested reference. And also for this verification, busbar manufacturers normally come to our aid.
The limits provided by the standard, under which it is not necessary to verify the short circuit, are the following:
- The rated short-time withstand current (Icw) or the rated conditional short-circuit current (Icc) not exceeding 10 kA r.m.s.
- If a current-limiting device is present and the limited peak current (Ipk) does not exceed 17 kA at the maximum allowable prospective short-circuit current.
- For auxiliary circuits only, if connected to transformers whose rated power does not exceed 10 kVA for a rated secondary voltage of not less than 110 V, or 1.6 kVA for a rated secondary voltage less than 110 V, and whose short-circuit impedance is not less than 4 %.
A study on short-circuit currents
Let’s better understand what the various short-circuit currents are.
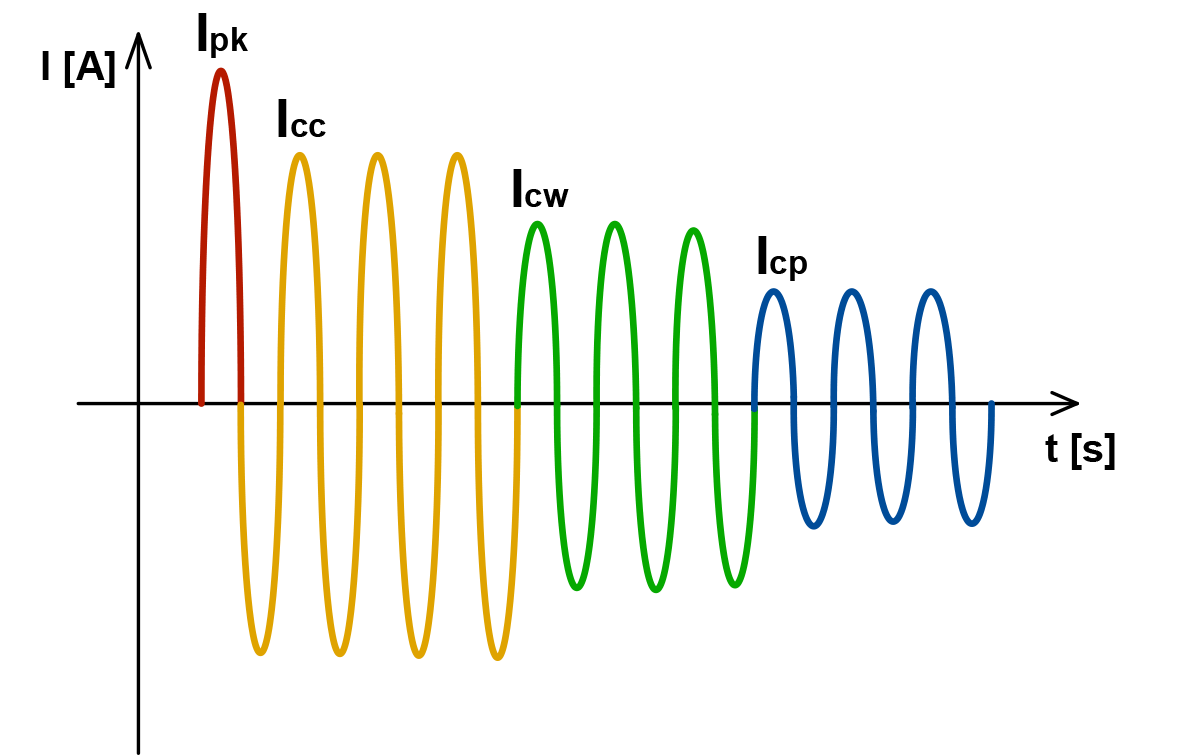
The trend of the short-circuit current over time. During the first fractions of a second, a peak (Ipk) appears, which then goes to fade, stabilizing at a certain value (Icp). The time required to reach this last current value is of the order of magnitude of 1s. In reality, the trend of the current is not symmetrical as schematized in the graph, but shifted to one side, becoming symmetrical only when Icp is reached.
Peak current
Ipk – in red on the graph. It is the absolute maximum value that the short-circuit current reaches at the beginning of the fault. It is possible to limit this current with limiting devices, such as fuses and switches. In this way, the peak current can be lowered below the threshold to avoid short-circuit verification.
Rated conditional short-circuit current
Icc – in yellow in the graph. It is the r.m.s. value of current (simplifying a lot, it is the current that gives the same effect of an equivalent DC supply) of short-circuit which the electrical panel must withstand until the protection device trips.
Rated short-time current
Icw – in green on the graph. It is the r.m.s. current relative to the short-circuit test for a defined time, without the tripping of protections. It means that no element of the electrical panel must be damaged by the passage of this current for a defined time. Normally 1s is used, but it may vary. It is also possible to assign different Icws for different times to the same panel.
prospective short-circuit current
Icp – in blue on the graph. It is the value the short-circuit current would tend to if it were not interrupted by the protection devices. We can see it as the steady-state short-circuit current after the initial amplified phase is damped. In practice, this current is never reached, as the protections trip to stop the fault.
The advantages of using a busbar system
As we have seen above, if we exceed the thresholds for which the standard requires verification, the first advantage lies in the ready-made tests that the busbar system supplier can give us, certifying our system. But is it convenient to use busbar systems even when we are below these thresholds? The answer is yes, because, as we will see shortly, the benefits are numerous.
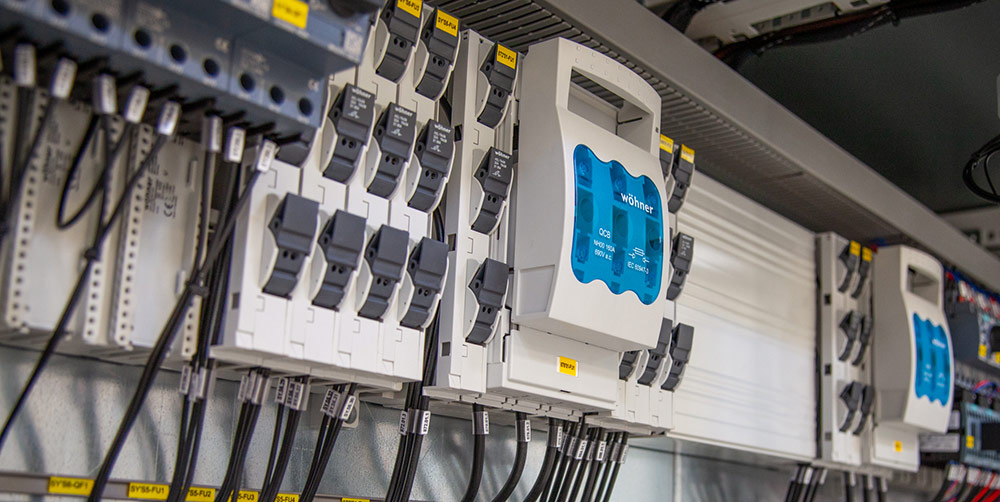
- Better short-circuit resistance. Regardless of whether we are asked for a short circuit test or not, a busbar system guarantees a higher short circuit resistance than wires and certainly also a more predictable behavior.
- Reduction of manpower hours. A wired system requires a longer work compared to the assembly of a busbar system, which leads to a reduction in labour costs.
- Small panel size. This aspect has a double advantage: a reduction in the panel costs and an advantage for the customer who will have a smaller occupied volume.
- Ease of expansion. The busbar systems allow easier and faster connections in the event of future additions, plus the facilitation given by the left free space.
- Less risk of overheating on the connections. The accessories are connected with spring systems, therefore they are not subject to loosening over time. This also eliminates the need for periodic checks of hardware tightening.
- Tidier aesthetics. Certainly, the aesthetics of the panel also benefit, showing a more orderly and clean appearance.
If we now look at what we have on the other plate of the scale, we find a higher cost of the material compared to a wired system. But, considering all we have on the pros plate, the scale continues to lean towards the busbar systems. Our suggestion, when making these evaluations, is to look at all the aspects and think about what will happen in the future, not stopping at the comparison of the mere cost of the material, which is only a point on a much longer list.